Which project
can we help you with?
Blasting, grinding, cutting, infilling – to achieve a perfect result our customers’ applications are as varied as our product range. Whether you are involved with highly technical precision engineering or work as a blasting contractor, we will find solutions to meet your individual requirements. Let us advice you.
Anti-Skid
In accordance with the relevant trade regulations for non-slip flooring at work, floors must have sufficient slip resistance in all industries and environments.
Equally, it must be ensured that sufficient displacement space is achieved so that aquaplaning hazards are reduced.
.
Blast Cleaning
With blast cleaning, the aim is to remove any unwanted residue or dirt from components.
A slight change in the surface properties of the component may be partially required.
A suitable abrasive and a gentle blast process ensure that no abrasion occurs, and that the part is only cleaned when treated.
Fettling
Casting cleaning – The risers (feeder) are removed from the castings by means of cutting grinding or cutting torches. The contour is then smoothed by grinding sharp edges, splinters, burrs and connection points. In order to remove the grinding marks and give the surface a uniform surface appearance, a final jet path takes place.
Depending on the casting material, a ferritic or austenitic round grain is blasted. The particle size is determined by the surface hardness and geometry of the castings as well as the possible system parameters.
Coated And Bonded Abrasives
The mineral crystals in an abrasive tool efficiently function as cutting edges to shape a substrate.
Fused aluminas and silicon carbides have proven to be particularly effective, possessing optimum properties for this application due to their hardness and sharp edges.
Deburring
During the production and machining of components by turning, milling or punching, edges/ratio are created which impair the functionality of the workpieces.
Deburring by blasting is a reliable and economical solution for the removal of these undesirable irregularities.
Rust Removal
Rust can completely destroy metals, so it is essential to remove it promptly and thoroughly from oxidised areas .
There are a variety of solutions to accomplish this, however rust removal by blasting has many advantages over other processes.
In addition to its low impact environmental-friendliness, this application is very precise, and gentle enough to fully preserve component sections.
Jeans Blasting
To achieve the popular vintage or used look of jeans, they are treated with an abrasive.
For a long time quartz sand was used for this process, but this led to dangerous silicosis, also known as “dust lung”.
Fortunately this is now banned, and Kuhmichel has alternative blasting media which are not harmful to the user’s health.
Do you have any questions?
Masonary Cleaning
Buildings are exposed to constant environmental influences and pollutants, which sooner or later lead to weathering. The result is soiled and discolored surfaces which are visually unattractive.
A cost-effective, environmentally-friendly, chemical-free solution is to clean buildings with the help of blasting media. This removes all types of contamination whilst keeping substance loss on the substrate itself as low as possible.
Matt / Satin Blasting
As the title suggests, this is a surface treatment which aims to create matt or satin surfaces.
These are a popular alternative to high-gloss surfaces because, in addition to the many practical advantages, they also impress with their high-quality appearance.
Precison Blasting
Precison blasting is a very gentle application which aims to thoroughly clean a component, whilst maintaining the substance of the substrate during the process.
Precision blasting treats the surface of a fine structure with the intention of refining the object, and requires a closely controlled grain size.
Paint Stripping
With paint stripping, the compromised paint layers are removed from a component by a blast process which ensures good adhesion for re-coating .
A popular area for this application is the restoration of classic cars, in which enthusiasts attach particular importance to authenticity.
Our high-quality reusable blast media allow effective and thorough paint stripping of various parts.
Polishing
Polishing requires a premium abrasive with a closely controlled grain size. The sizing does not allow for any tolerances, and must correspond exactly to the required specification, otherwise scratches may occur in the polishing process.
When it comes to polishing, Kuhmichel is a renowned supplier throughout Europe.
Our polishing customers rely on our consistently high-quality abrasives, which are supplied with the relevant documentation.
Shape Blasting
Compressive residual stresses are induced in the component by blasting or peening.
With thinly-walled components, this results in forming and simultaneous hardening.
Through this process, highly stressed components can be shaped as desired, and fatigue strength can be improved.
Sand Removal
Parts cast in sand moulds must undergo a post-treatment step to free them from the adhering sand. This is done to a large extent in blast wheel blast cleaning systems in which round metal grit made of cast steel or stainless steel is used. The decisive factor in the choice of abrasive is whether the casting itself consists of ferritic or ferrite-free materials.
The optimum ratio of volume to the surface of the round grain achieves the desired impact force. Since a complete cleaning of the workpieces is just as important as a homogeneous covering of the surface, the choice of grain size plays a major role.
Shot Peening
During shot peening, residual compressive stresses are induced by using round grain (shot).
This causes the first tenth of a millimeter of the component edge layer to solidify.
Dynamically stressed components, e.g. springs, gears, axle parts and turbines, may through this process achieve a significantly longer service life, and also have their dimensions reduced.
Vapour Blasting
The term vapour blasting refers to a gentle blasting application, which removes impurities from a component but does not attack its substance.
Many people know this blasting process from the cleaning of buildings or the restoration of vintage cars.
Structural Blasting
Structural blasting creates a homogeneous surface which meets the highest technical and optical requirements, by defining and roughening the component.
With the many possibilities of this application, it is crucial to determine both the right blast media and the right blast process in order to achieve the desired parameters, such as roughness, slip resistance, and degree of gloss and brightness of the surface.
Surface Finishing
The surface finish is usually the final step in a long chain of machining processes.
The main aim here is to create an optically finished product with a uniform, high-quality surface finish.
Surface Preparation
Blasting prepares the surface for subsequent coating or other treatment. The adhesion between the component and the coating is considerably increased by blasting with an angular abrasive. The surface roughness created by this process will increase the surface area, and offers the coating more surface area for adhesion.
Surface Preparation
The aim of a coating is to have a positive effect on the properties of workpieces, both chemically and physically. An important criterion for assessing the quality of coatings is their adhesive strength. It describes how well the applied layer holds on to the workpiece. This parameter can be massively influenced by processing the workpiece with an angular blasting medium.
The blasting process results in roughening of the workpiece. The resulting surface topography guarantees a considerable improvement in adhesion, resulting in a significant increase in the quality of the workpieces.
Sweep Blasting
The term sweep blasting refers to a special form of blasting in which, for example, galvanized surfaces are carefully roughened in order to improve their adhesive strength for subsequent coatings.
Sweeping differs from surface preparation in that the abrasive hits the surface at a very acute angle.
In addition, reduced pressure is used to carefully roughen the zinc layer without penetrating it.
To ensure the exclusion of corrosion, only mineral and iron-free abrasives, such as fused alumina or garnet sand, are used.
Water Jet Cutting
By adding abrasive material to the water jet cutting process, extremely hard materials can be cut without heat generation.
The water/abrasive mixture is accelerated to almost the speed of sound at a pressure of up to 6400 bar.
A high degree of precision, high cutting speeds and short set-up times characterise this technology.
Kuhmichel offers suitable abrasives for all systems and applications.
Do you require assistance?
We will be happy to help you!
Contact
Any Questions?
This site is protected by Google reCAPTCHA.We use an extra cookie for its essential functionality.Please click on “Agree” to accept.
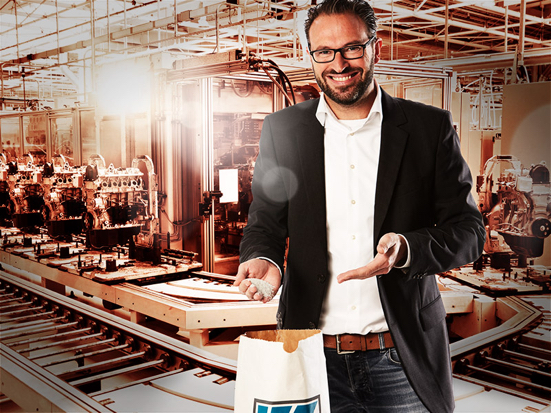